Using AI to cut industrial carbon emissions
How AI is saving millions of tonnes of carbon from the single largest industrial emitter: cement
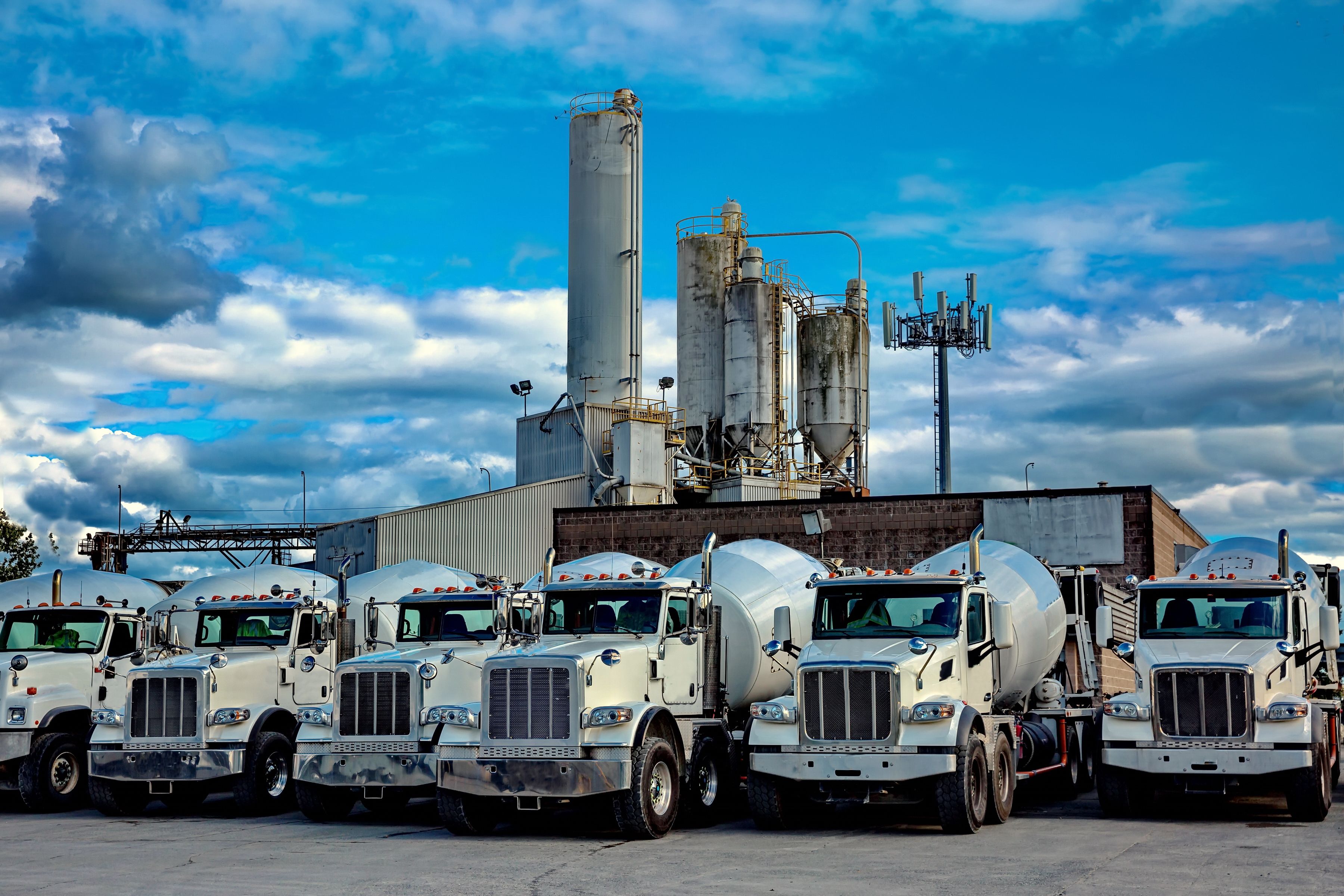
“Cement production matters to all humanity. It is the most important area of industrial activity for reducing carbon emissions, the key driver for climate change and global warming.
“It is responsible for a greater share of carbon emissions than deforestation, global shipping and aviation combined. Cement is the active ingredient in concrete – the most widely used material by humans, after water.”
- Three technologies to reduce climate change, Carbon Re
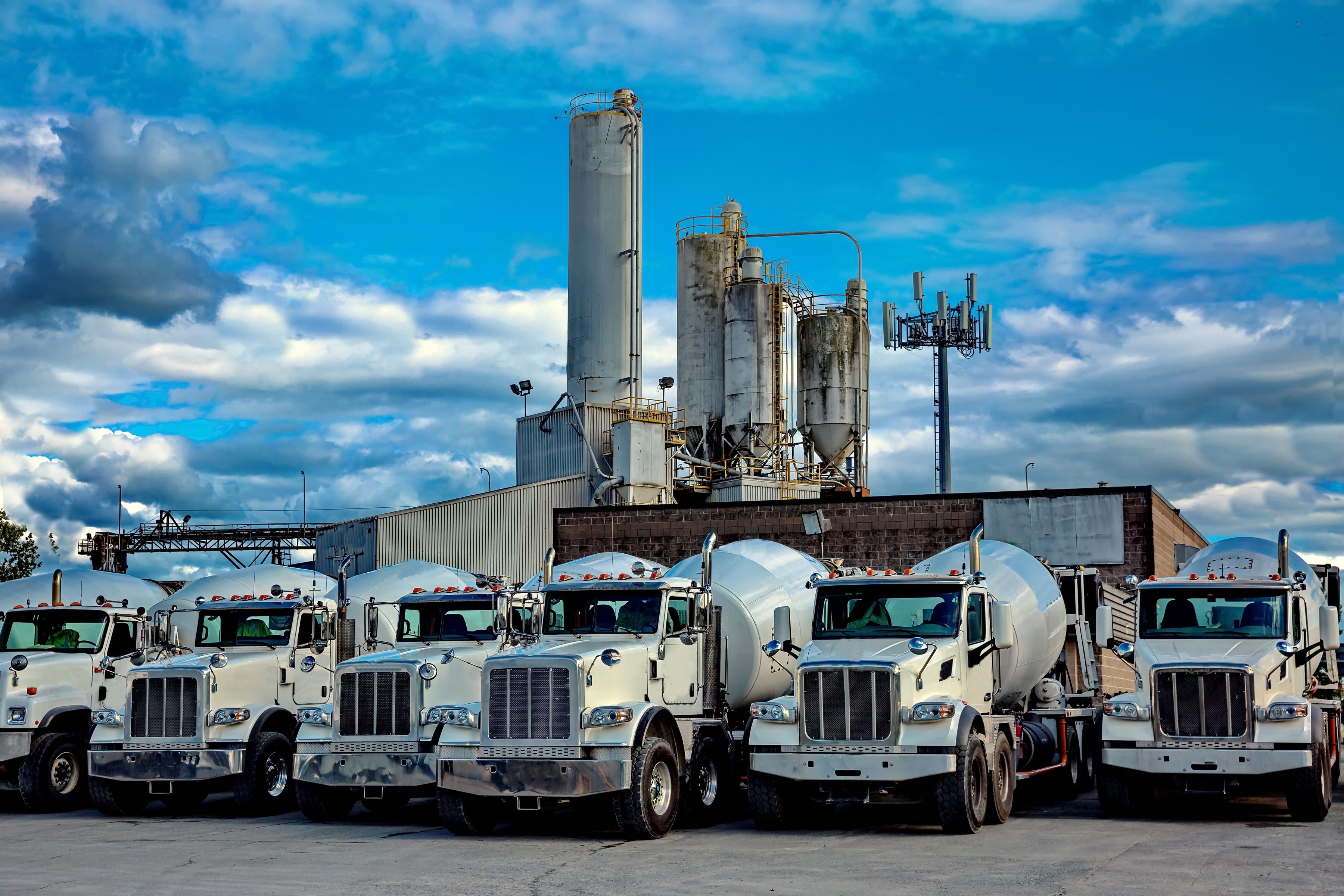
Cement factory. Image credit: Alex_533 (iStock)
Cement factory. Image credit: Alex_533 (iStock)
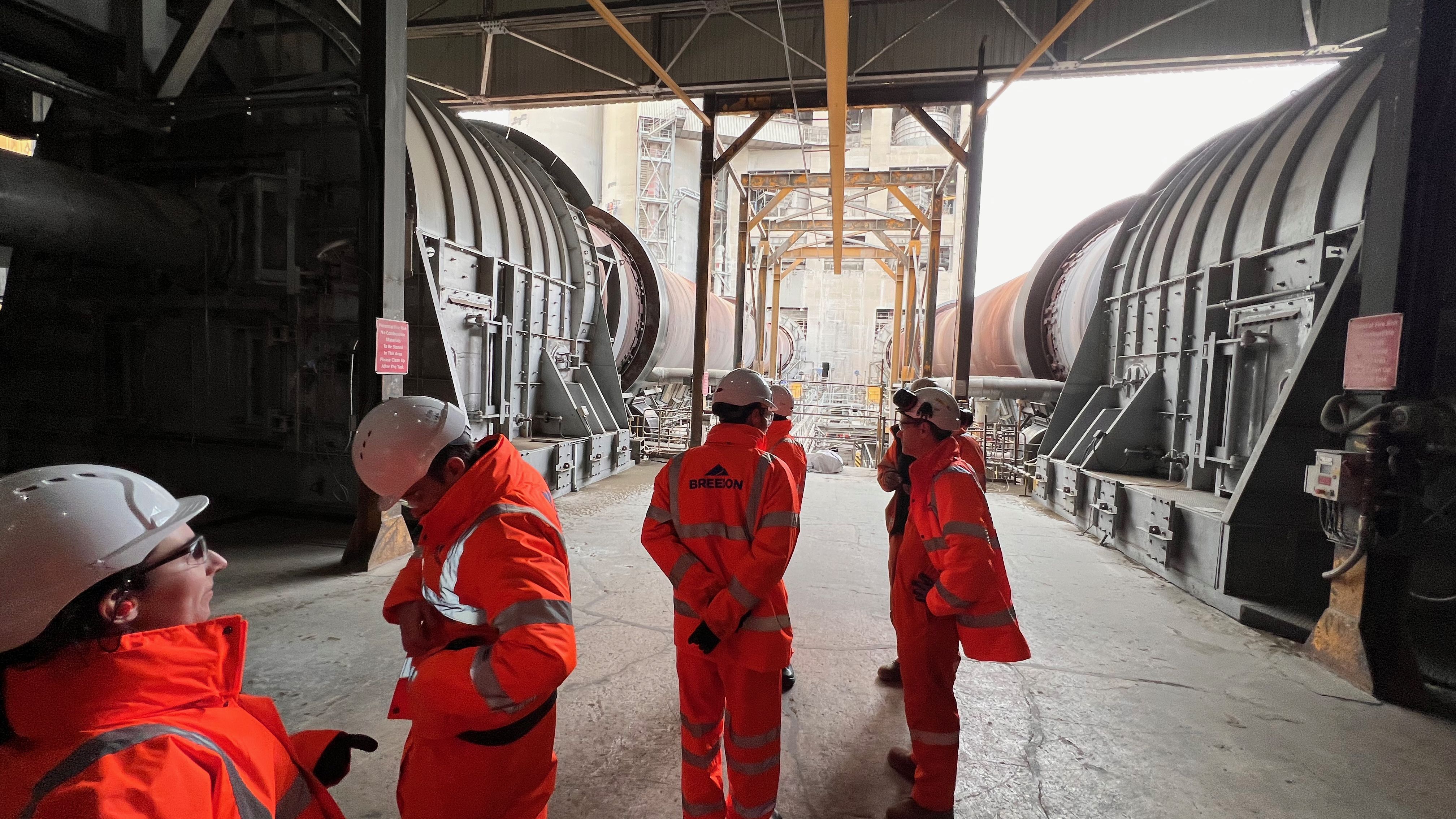
Hope Cement Works operates two kilns, the two long cylinders seen here in the background. To make cement, the raw materials are heated to around 1450 degrees centigrade by burning vast amounts of fossil fuels. This process produces nearly half of the carbon emissions associated with cement production. Image credit: Carbon Re
Hope Cement Works operates two kilns, the two long cylinders seen here in the background. To make cement, the raw materials are heated to around 1450 degrees centigrade by burning vast amounts of fossil fuels. This process produces nearly half of the carbon emissions associated with cement production. Image credit: Carbon Re
While politicians often focus on the comfortably distant goal of reaching global net zero carbon emissions by 2050, the science is clear that reducing emissions immediately is the only way to avoid a catastrophic and irrevocable rise in global temperature.
While safe and viable alternatives to cement are still being explored, our societies would struggle to function without cement-based concrete for our buildings, roads, bridges and dams.
This places a huge responsibility on the shoulders of cement producers across the world to find ways to reduce their emissions – a task for which Dr Aidan O’Sullivan of the Bartlett School of Environment, Energy and Resources has helped develop an important new tool.
Aidan’s new startup, Carbon Re, has launched an artificial intelligence (AI)-driven software platform, Delta Zero, which allows cement producers to optimise their processes and reduce their carbon emissions by up to 10%.
“Focusing on the heavy industries as a concentrated source of emissions... would make a significant impact - potentially gigatons of impact - on climate”.
Modernising our most vital industries
For several reasons, the cement industry is well placed to benefit from the latest advances in AI and machine learning.
“I think this section of manufacturing is quite behind the curve in terms of digitalisation and automation.
“If you look at automotive, or more high-value manufacturing, they’re already using a lot of digital technology to improve their operations.
“This is the direction of travel, and the future of the industry – bringing savings in process and engineer time, reducing downtime and quality variation, and all the while saving energy as well.”
Cement production requires extremely high temperatures, which are achieved by intensive use of fossil fuels. To do this safely, cement plants have to monitor a wide range of variables round the clock – which means they are already gathering the data needed to feed the AI.
“We don’t install any hardware on site – all that technology is already in place.
“The great thing (kind of) about cement factories is they’re really incredibly dangerous.
“With temperatures around 1,500 degrees, they have a huge number of sensors – they need this equipment in place in order to function.”
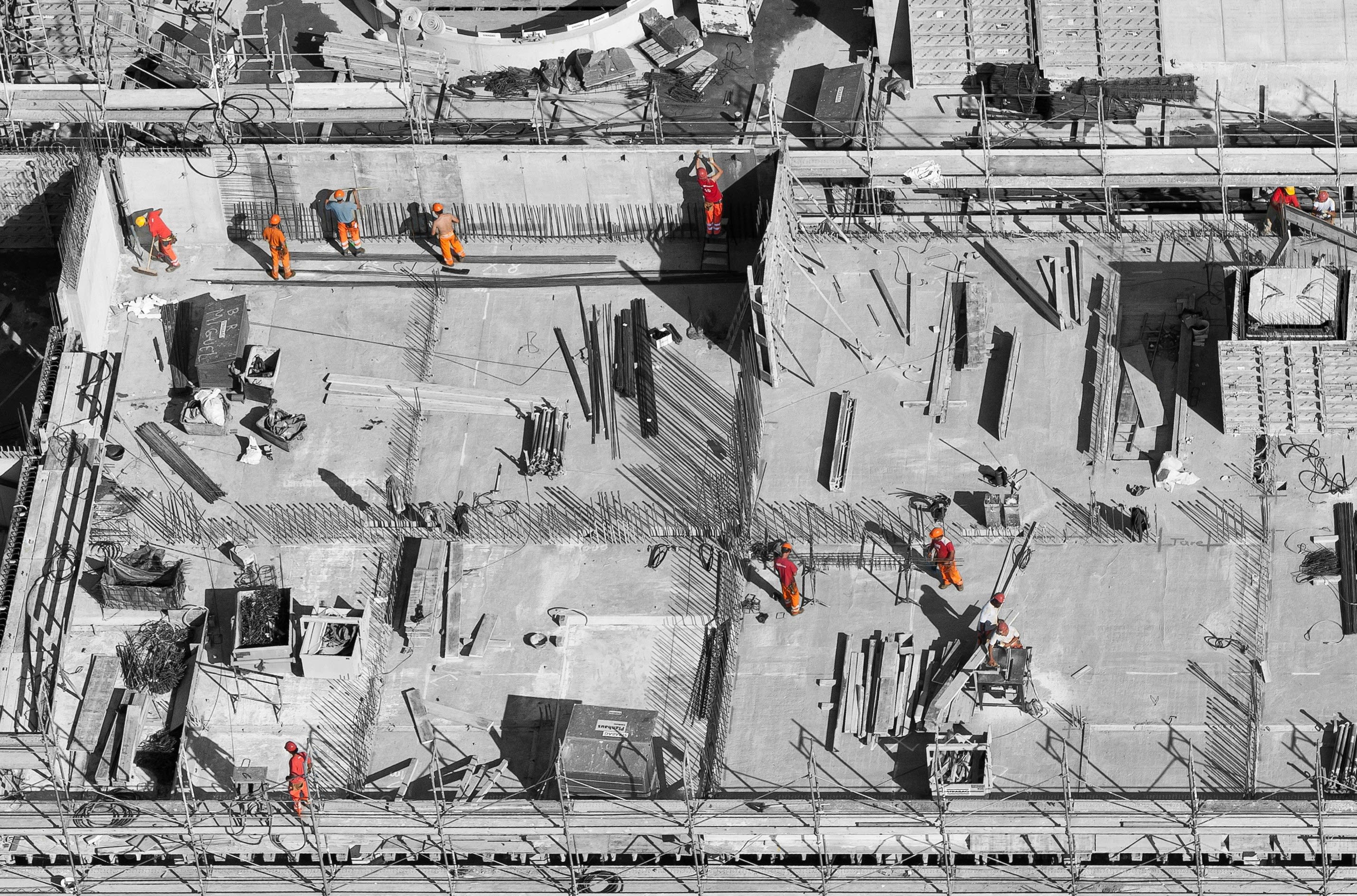
Going beyond human capabilities
Importantly, Delta Zero’s improvements to cement production efficiency also come with distinct advantages for the personnel running the plant.
Cement plant operators are overwhelmed with information. During their initial research, Aidan and Dan observed for themselves the complexities confronting operators, with process control alerts going off every 15 seconds.
“The job of the operators is getting more and more complex, as they’re being asked to reduce carbon emissions and do even more things at the same time.
“They have to try and oversee everything – blockage issues, quality control, production targets, predictive maintenance. It’s challenging.”
When it comes to supporting these complex processes, existing software solutions in the cement industry are of limited use. Any change to the type of fuel used, production processes or output targets requires a complete redesign of the rules-based system involved.
Aidan likens them to the autopilot systems found in some modern cars.
“They can keep you in the same lane and keep you driving forward. But they don’t actually tell you where you should be going.”
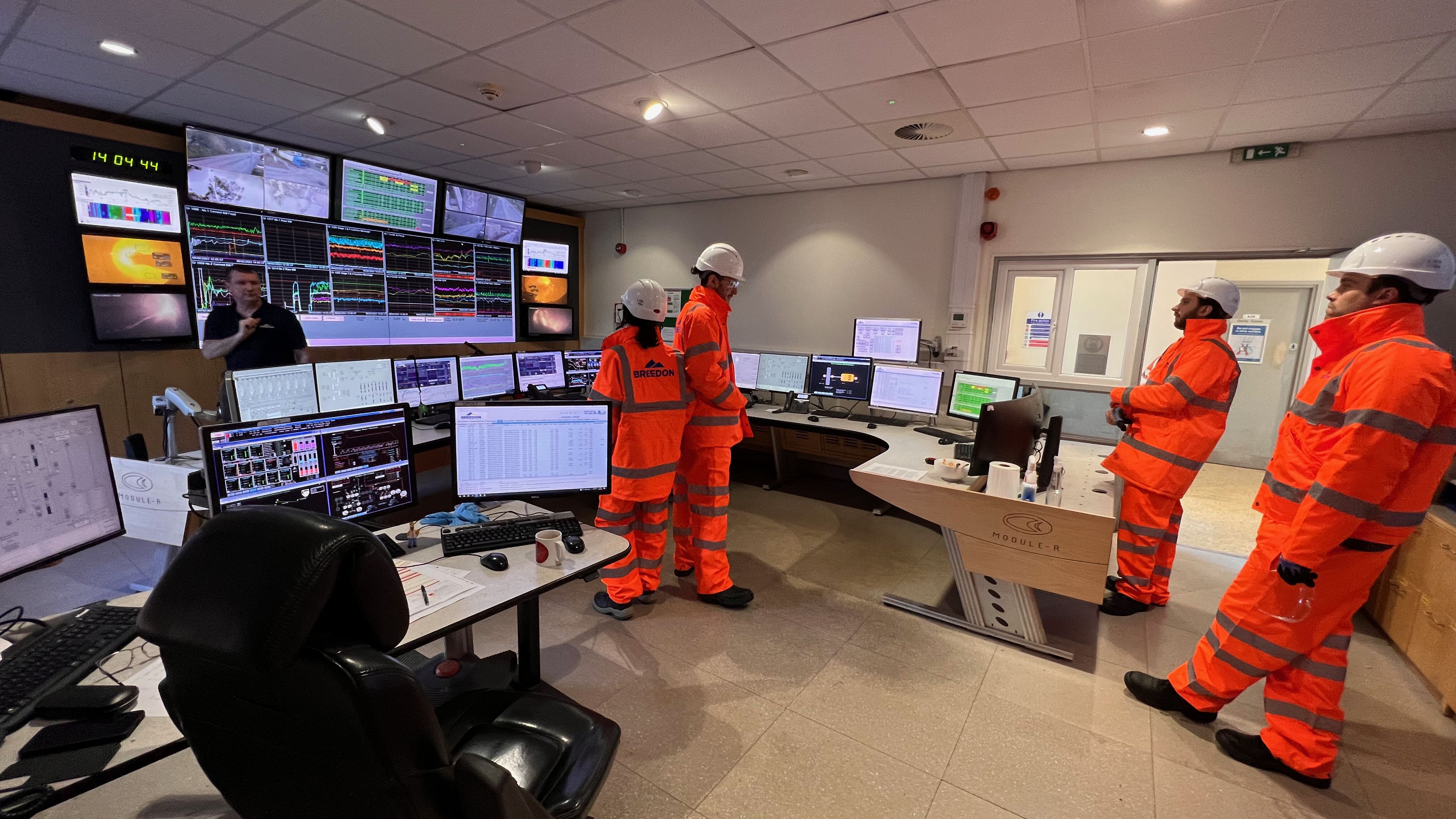
Real-time virtual management
Delta Zero uses reinforcement learning (RL), interacting with a digital twin of the cement plant created using sensor data streamed from the actual plant.
The AI experiences a multitude of scenarios based on the complex interactions between plant processes. Within 24 hours, Delta Zero will have simulated roughly 100 years of cement plant operation.
These simulated experiences provide the AI with the data to make strategic decisions to optimise plant processes, according to a dynamic and flexible set of ‘reward’ functions.
These real-time recommendations allow cement plants to work far more responsively, reducing both fuel wastage and carbon footprint.
“Fundamentally, what we want to control is the energy going in – the fuels. Firstly, we want to act on those, so instead of putting in eight tonnes an hour, we can put in seven tonnes for the same output.
“There are also mechanical levers we can pull – fan speeds, fuel flows, fuel rates, material flow speeds.”
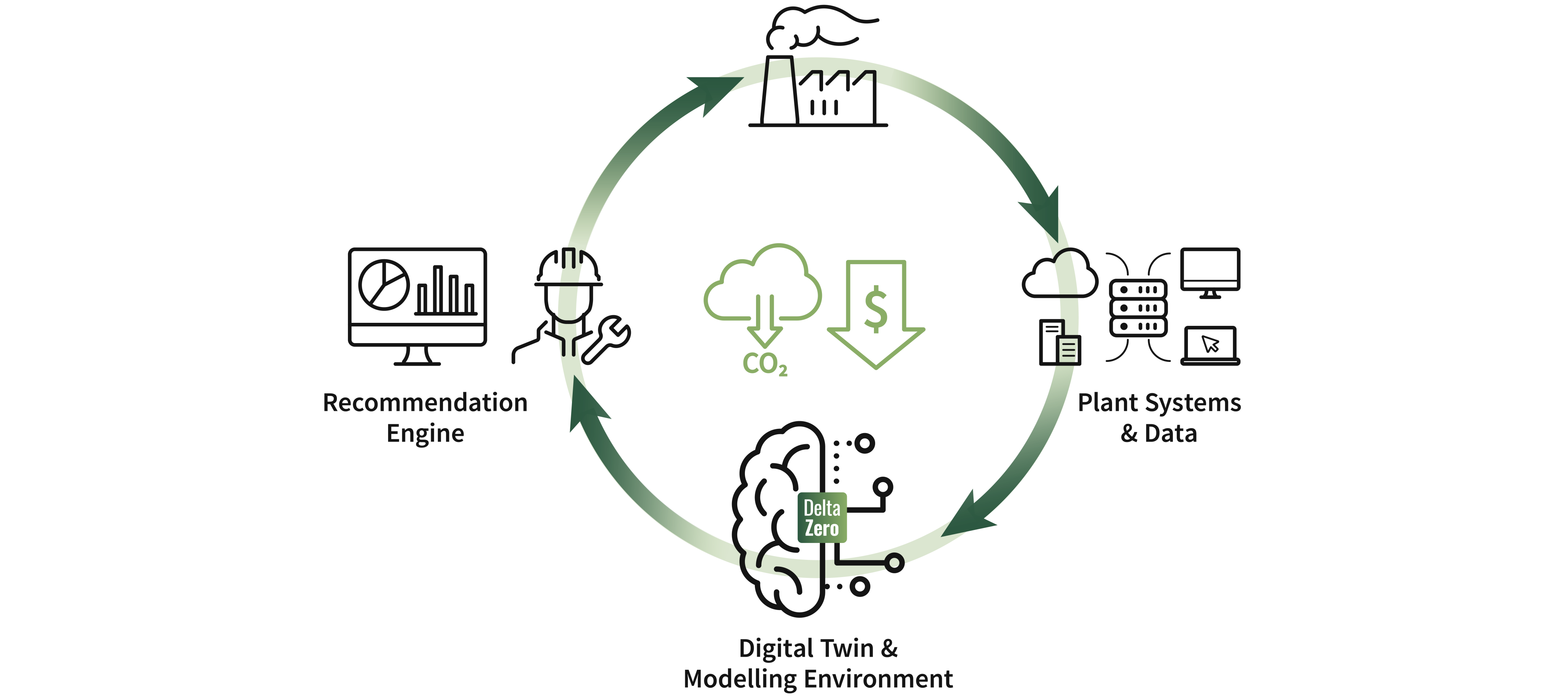
Delta Zero can operate as a human-in-the-loop solution, where the plant operator maintains control over production processes. Image credit: Carbon Re
Delta Zero can operate as a human-in-the-loop solution, where the plant operator maintains control over production processes. Image credit: Carbon Re
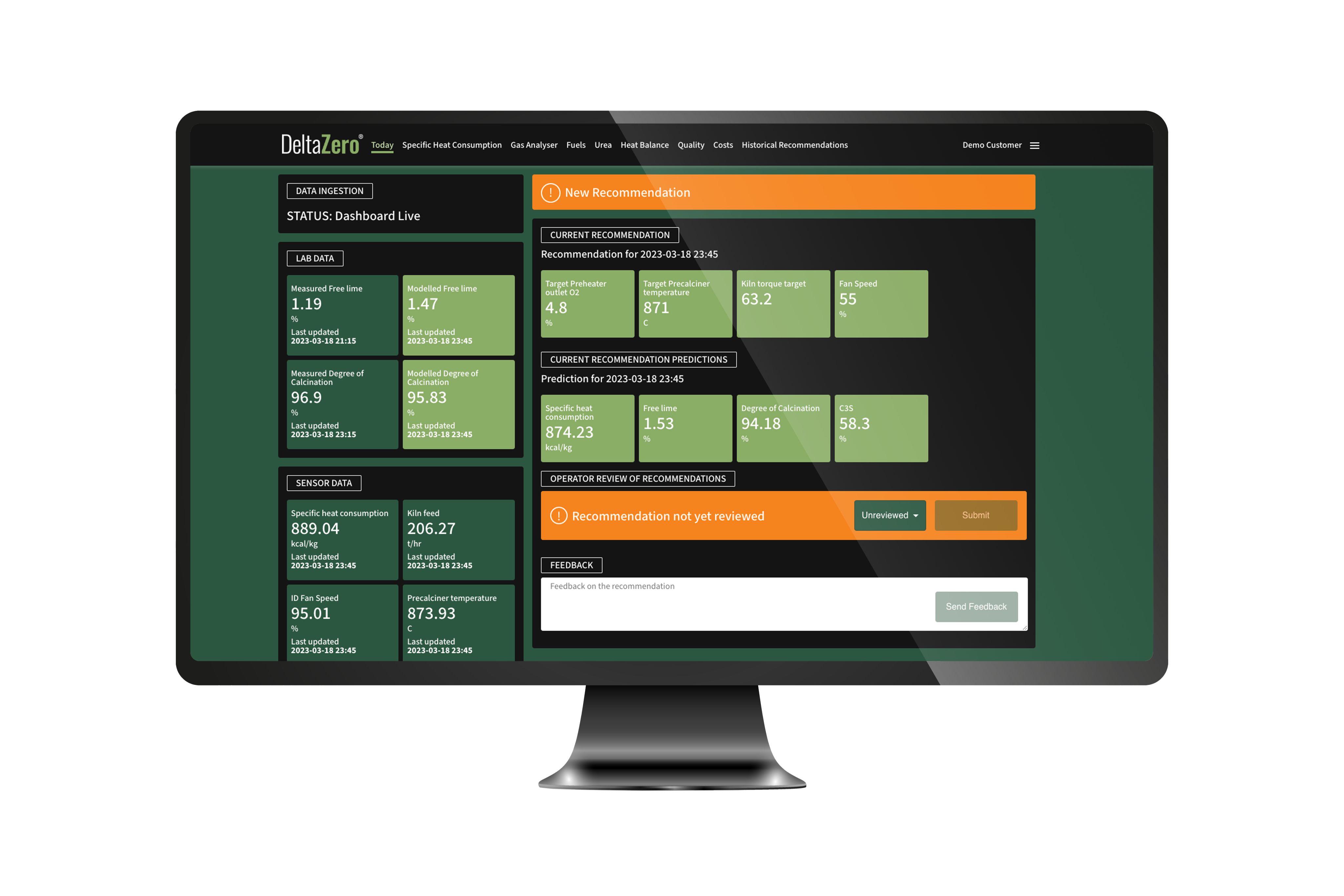
When a user logs in to Delta Zero, the platform opens to the Today page, containing a dashboard summarising the state of current plant data, modelled data, and the newest recommendation. Image credit: Carbon Re
When a user logs in to Delta Zero, the platform opens to the Today page, containing a dashboard summarising the state of current plant data, modelled data, and the newest recommendation. Image credit: Carbon Re
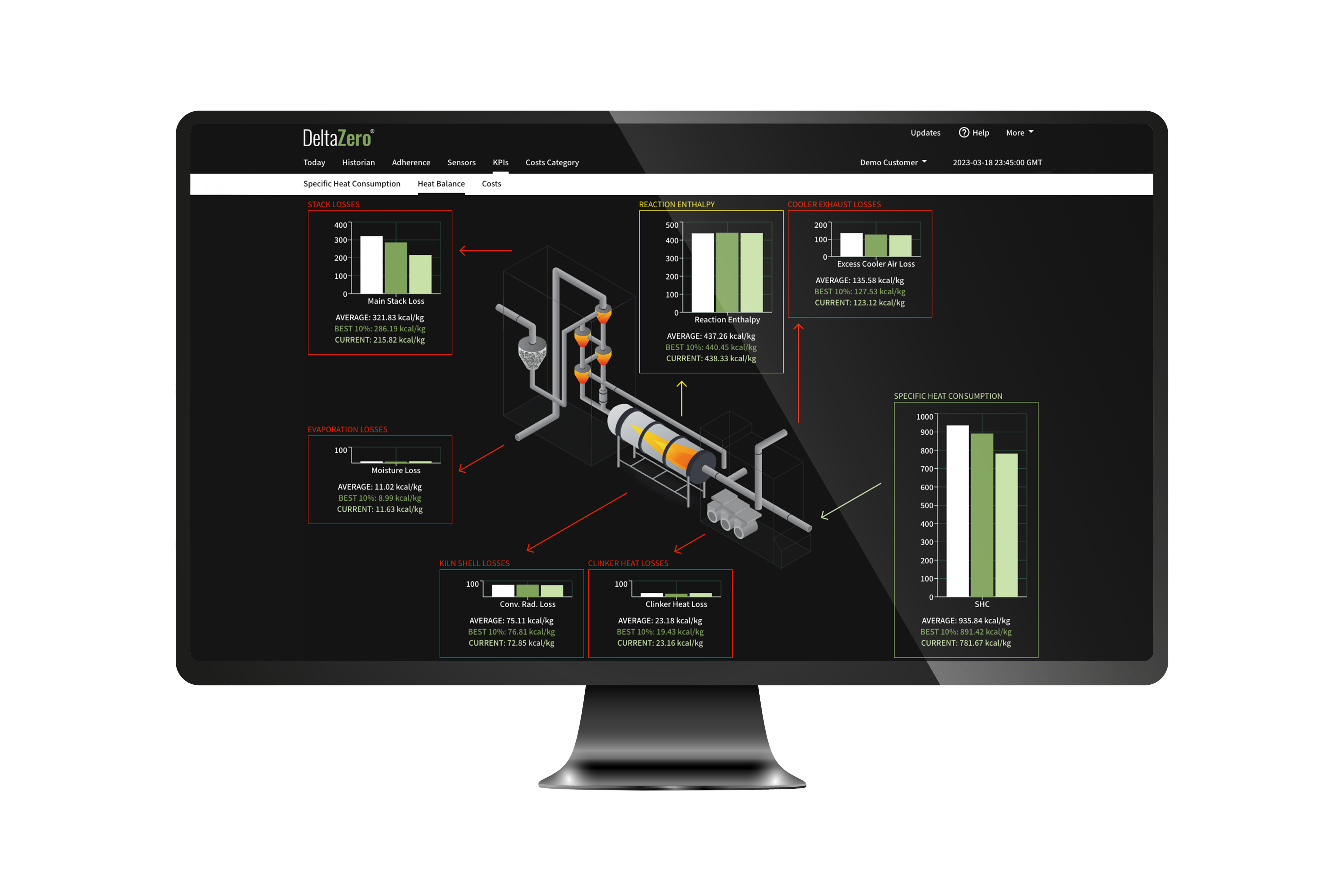
The Heat Balance data reports the plant’s energy inputs and losses, comparing the current state to historical data. Image credit: Carbon Re
The Heat Balance data reports the plant’s energy inputs and losses, comparing the current state to historical data. Image credit: Carbon Re
Automatic improvements
Carbon Re are still amassing the evidence required to trigger widespread adoption of Delta Zero across the cement industry. Though they’ve been piloting the platform for two years with cement plants in Canada, India and South America, the latest iteration of Delta Zero has only been in operational use since January 2023.
Aidan is hugely encouraged by the way plant operators are increasingly using Delta Zero to continuously automate processes, rather than taking recommendations in manual mode.
“With existing plant management systems, operators tend to turn them off and on at will – operator preferences get factored in, and systems get switched off for eight hours or more.
“However, we’ve seen our systems stay online more or less continuously, with closed loop control setups driving systems in the plant based on Delta Zero predictions.”
The AI’s choice of action is influenced by the reward function, which can be tailored to induce the desired behaviour from the plant’s machinery and processes.
This means Delta Zero can also be configured to account for a whole range of local factors that impact on plant processes, from the availability of less carbon-intensive alternative fuels, through to missed production targets and unexpected shutdowns.
“We can basically take the priorities of different plants and operators and tune the model towards them. If an operator is trying to increase the amount of biomass they’re using, we can adjust for that, or focus on just maximising production and maintaining quality – the flexibility is there within the system to handle those kinds of issues.”
Solutions for the biggest problems
Despite the inevitable inertia faced by innovators attempting to introduce new technologies in any well-established field (and the comparative lack of IT infrastructure deployed by smaller cement producers), industry response to Carbon Re and Delta Zero has been enthusiastic.
Carbon Re are currently working with five plants globally, and are in discussions with several more.
“It’s funny...we thought we’d get a lot more resistance than we’ve encountered,” Aidan reflects. “But generally, people are positive and open to the technology.
“There’s an understanding that the industry has to change. People are looking for solutions to the problem of cement carbon emissions, and it feels like we’ve got a lot of support from the industry to build the technology and solve some of these problems.”
With the looming threat of costlier, more punitive carbon tax levies for heavy industries in the UK and elsewhere, there are additional financial pressures on cement producers to adopt solutions such as Delta Zero, too.
Meanwhile, Aidan and the Carbon Re team are already looking for ways to increase their impact, by adapting Delta Zero for other heavy industries.
“Steel, ceramics, glass and paper are also in our sights as well.
“After cement, steel would be our primary focus. Steel produces about 8% of global emissions – roughly the same order of magnitude as cement, but whereas there are around 3,600 cement plants in the world, there are only 600 steel plants.
“So each of those steel plants is making a huge contribution to carbon emissions. We’re seeing transitions to less carbon-intensive processes in the steel industry, such as electric arc furnaces, but we still need to know how to run those processes effectively, too.
“AI can help with that learning curve.”
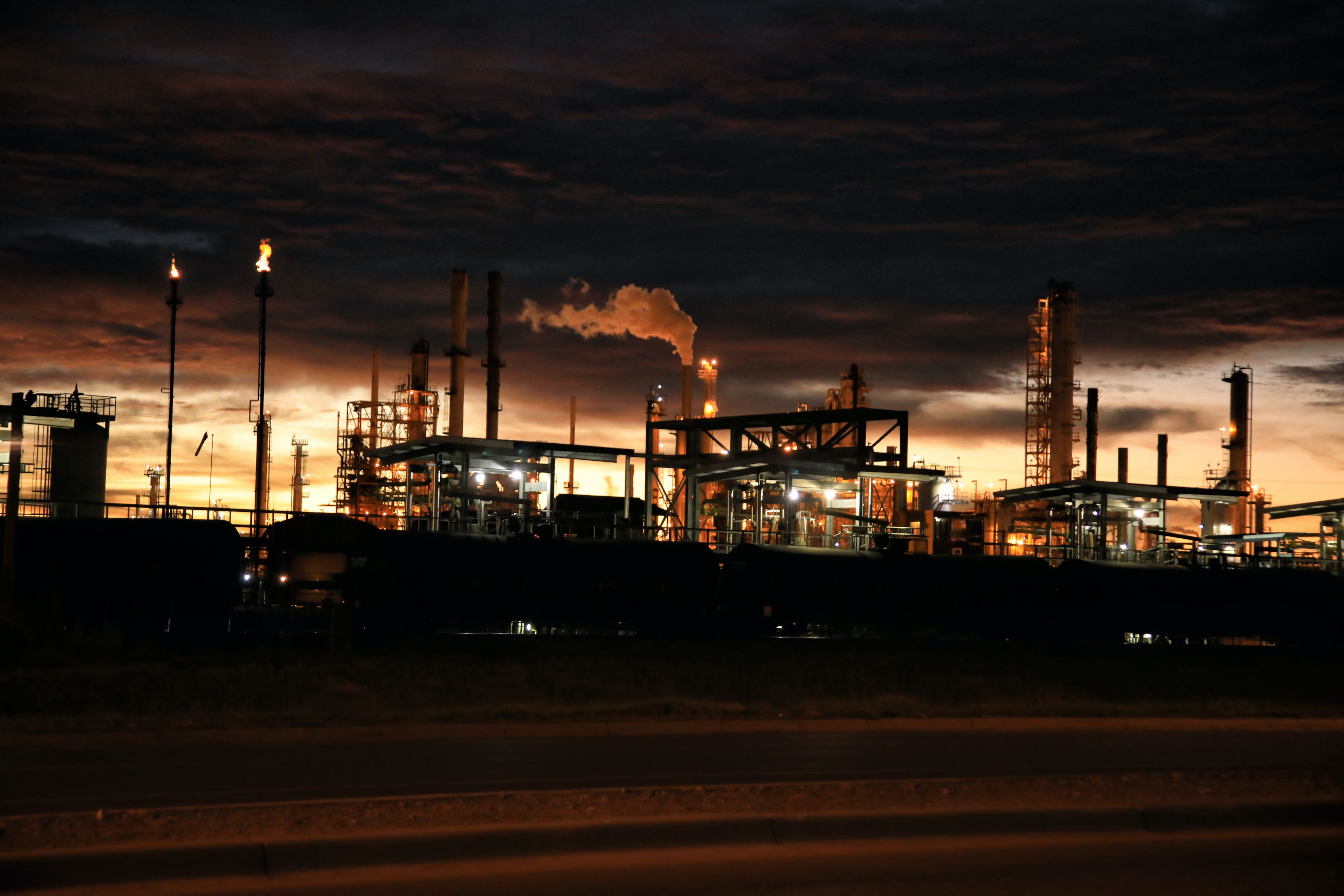
“There’s an understanding that the industry has to change. It feels like we’ve got a lot of support from the industry to build the technology and solve some of these problems.”
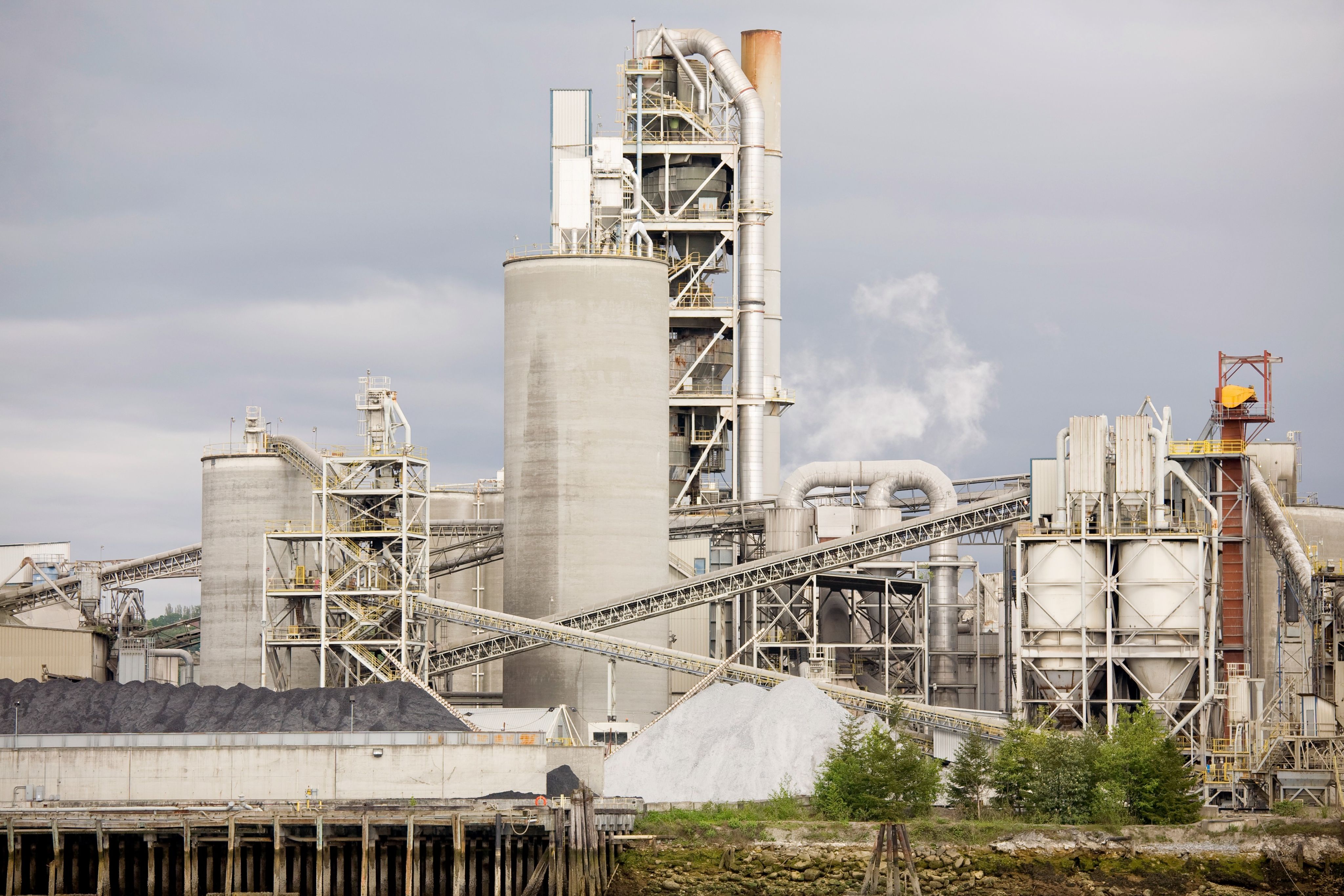
About the author
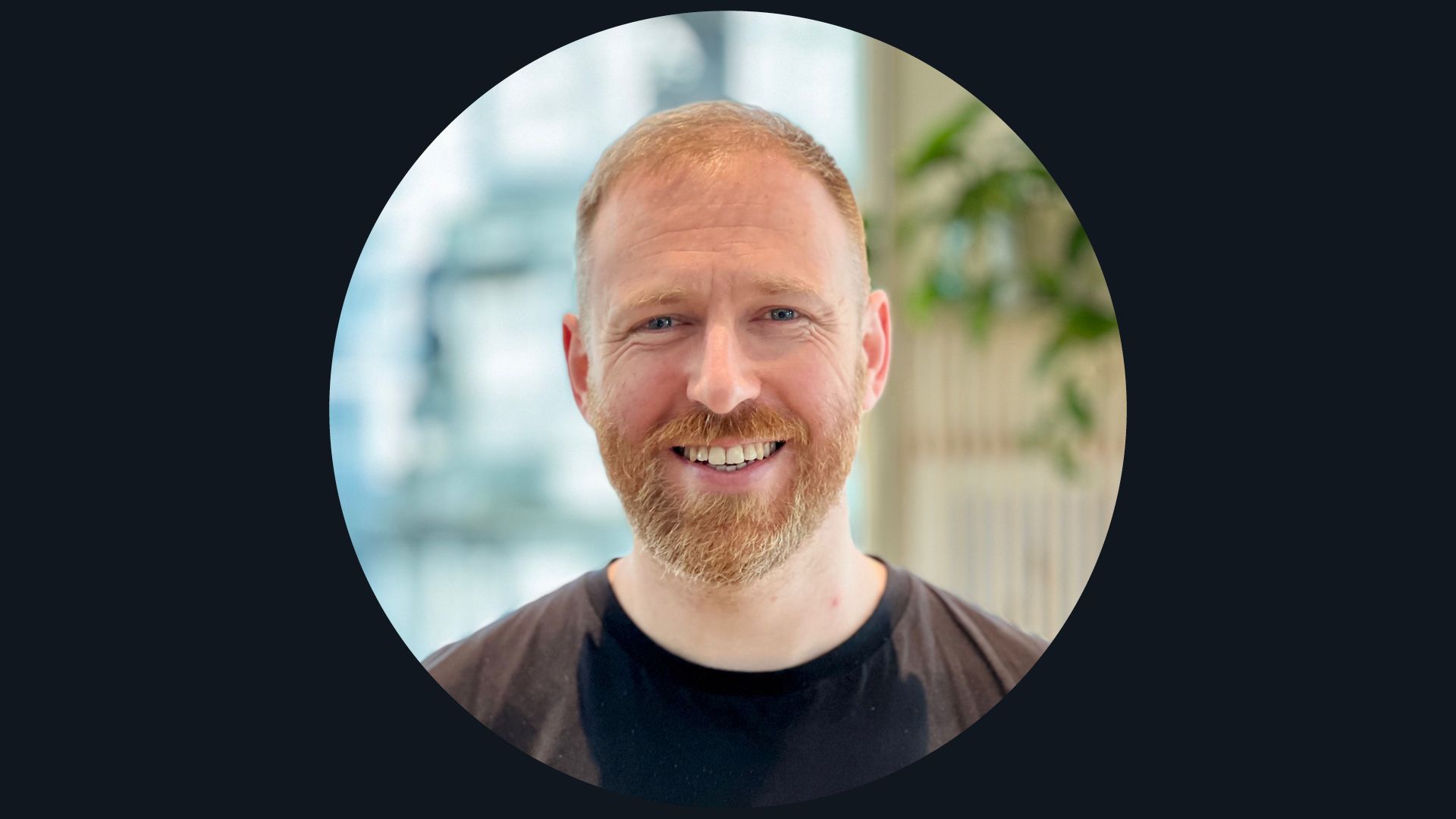
Dr Aidan O'Sullivan
Associate Professor in Energy and Artificial Intelligence, UCL Energy Institute, The Bartlett School of Environment, Energy and Resources
Aidan leads the Energy Systems and Artificial Intelligence Lab and the UCL Energy Institute's Data Analytics research theme. He is also the founding course director of the Energy Systems and Data Analytics MSc, an innovative degree that combines the study of energy systems and sustainability with data science and machine learning.
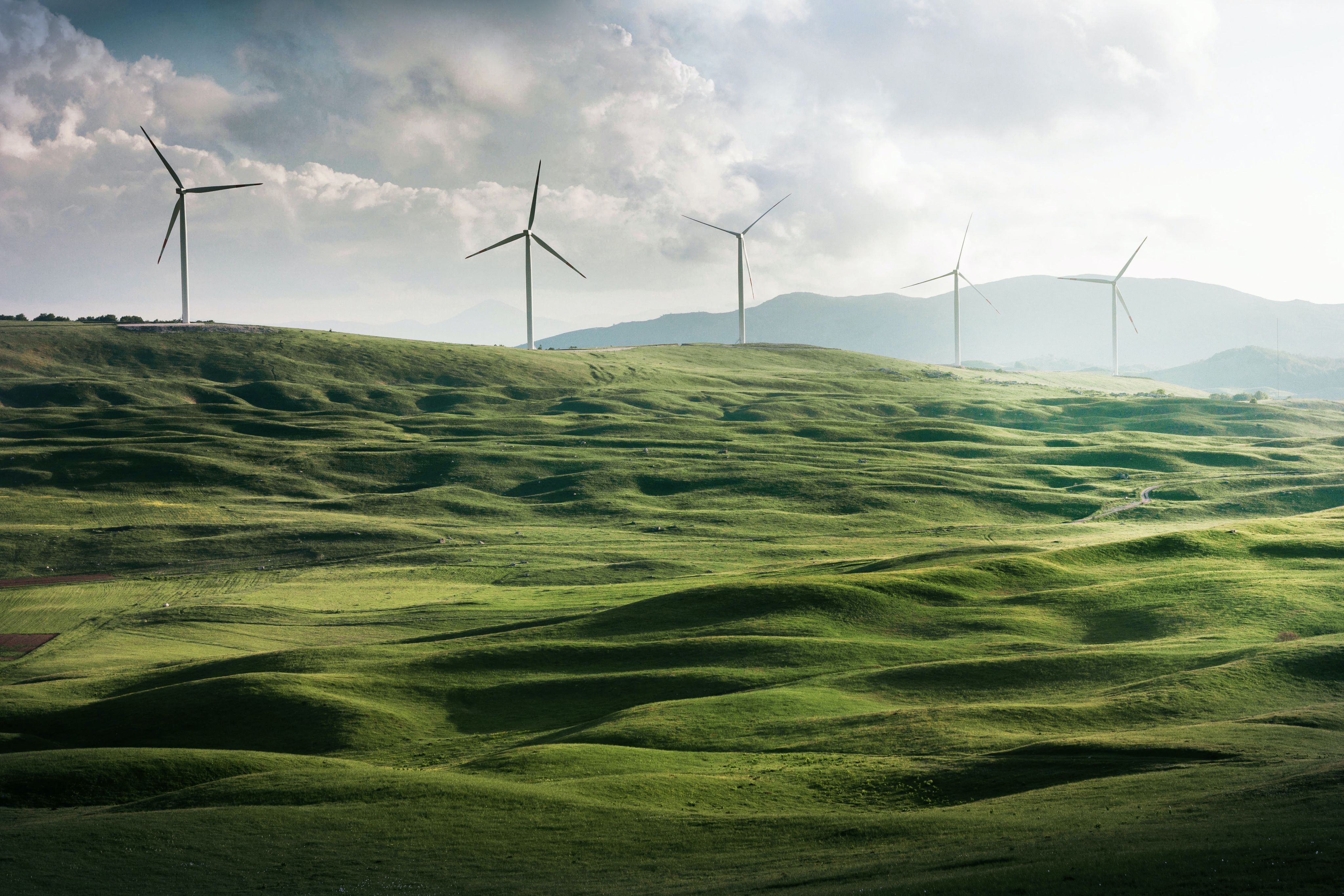
Photo by Appolinary Kalashnikova on Unsplash
Photo by Appolinary Kalashnikova on Unsplash
Learn more about Energy Systems and Data Analytics
Our industry-leading master's degree in Energy Systems and Data Analytics enables you to study energy systems through the lens of advanced data analytics, and unlock the transformative potential of big data to reshape the energy sector.
Story produced by All Things Words
© UCL The Bartlett 2024